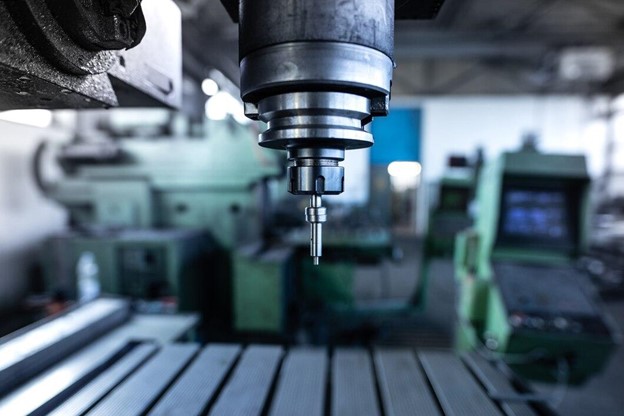
In the competitive world of manufacturing, precision and efficiency are paramount.
From the aerospace to the automotive industries, every industry relies on components that conform to exacting specifications.
CNC Milling Services have become the backbone of modern manufacturing, enabling the creation of intricate parts with unmatched accuracy and repeatability.
By automating traditional milling processes, CNC technology has transformed the way components are produced, combining speed, precision, and cost-efficiency.
B&K Precision Machining is one such leader in this domain, and CNC milling epitomizes their capabilities.
As part of its value proposition, the company optimizes manufacturing workflows with a seamless process from drawing submittal to finished parts.
It aims to assure manufacturers of quicker turnaround times, better quality, and lower cost.
These specifications, in turn, will eventually drive new innovations across industries.
What Is CNC Milling?
CNC (Computer Numerical Control) milling is a process in which material is removed by cutting tools from a workpiece under the control of computerized controls, forming some sort of desired shape or feature.
Unlike manual milling, CNC machines are guided by precise digital instructions that enable unparalleled consistency and complexity.
From metals, plastics, and composites, modern CNC milling machines can work with almost all types of materials, making them indispensable in industries requiring customized, high-quality components.
Be it small-scale prototypes or full-scale production runs, the versatility of CNC milling ensures it will continue as a cornerstone of contemporary engineering into the foreseeable future.
CNC Milling: Innovating Manufacturing
Manufacturing has always remained one of those industries where innovation plays a major role, and it is no exception with CNC milling.
Advanced software integration, multi-axis capability, and automatic tool change have redefined the possibilities in part production.
● Complex Geometries: multi-axis CNC milling makes it possible to produce those intricate designs that earlier were impossible or too costly to produce. Components featuring curved surfaces, internal channels, or sharp angles can be manufactured with ease.
● Improved Material Utilization: CNC milling reduces waste by optimizing the cutting process. Digital simulations ensure minimal material usage without compromising quality, thus aligning with sustainable manufacturing overviews.
● Scalability: from single prototypes to batches of thousands of identical parts, CNC milling scales up or down in response to production demands. This is important for industries such as medical device manufacturing, where precision and consistency are non-negotiable.
The Impact of CNC Milling on Engineering Design
Engineering design has also evolved along with CNC milling. With the ability to make the parts with micron accuracy, the sky’s the limit for engineers in innovating.
From lightweight aerospace components to compact electronic housings, once unthinkable ideas can be materialized by CNC milling.
Furthermore, the rapid prototyping capability from CNC machines shortens the development cycles.
It enables engineers to test designs, iterate, and refine products at a speedier rate than ever before, shortening time-to-market, and keeping their competitive edge in specific industries.
Smoothening Production Processes
CNC milling improves not only the quality of a single part but also the whole process of manufacturing itself.
Companies such as B&K Precision Machining are instrumental in this respect. By providing the CNC parts and components on time, they enable the manufacturers to focus on assembly and final production rather than bother about the delay in the supply chain.
The digital nature of the process also makes communication easy. Files are shared with ease and can be adjusted to avoid errors while trying to achieve the desired product.
This integration of technology and manufacturing know-how best describes how CNC milling achieves efficiency and reliability.
Applications Across Industries
CNC Milling is versatile and finds its application in most industries, from:
● Aerospace: precision is paramount in this industry where parts have to withstand extreme stress. CNC milling creates strong, lightweight parts for turbine blades, brackets, and structural components.
● Medical: special implants, surgical instruments, and diagnostic tools in medical all have specific dimensions and require biocompatibility. Computer numerical control milling ensures they receive the highest quality.
● Automotive: from the manufacturing of engine pieces to interior details, the basis of CNC milling lies in creating high-performance, durable auto parts.
● Consumer Goods: in consumer goods, CNC milling plays a big role in producing moulds for the mass production of goods that demand uniformity and efficiency.
Future Trends
While numerous advantages exist with CNC milling, there are several challenges, too.
Expert operators, maintenance, and initial setup costs may be something out of the question for some manufacturers. A lot of these concerns are going to be addressed with upcoming developments in automation and AI.
Yet, in the future, the integration of CNC milling machines with other technologies, such as additive manufacturing, or 3D printing, is going to advance even further.
Hybrid systems that combine subtractive and additive processes may offer new design and production opportunities, extending the capabilities of CNC technology even further.
With the addition of real-time monitoring and predictive maintenance tools, CNC milling machines will also be more productive and reliable.
IoT technologies will enable manufacturers to reduce such downtimes and further optimize their production schedules effectively.
Conclusion
CNC milling has truly reinvigorated manufacturing in terms of accuracy, scalability, and speed unimaginable in the past.
From the small enterprise level to large-scale international businesses, the advantages of CNC technology go even further to innovate and improve the working aspect of an industry altogether.
Companies like B&K Precision Machining continually work on fine-tuning their processes, adding state-of-the-art technologies.
In short, the outlook for CNC milling does not look brighter. It is through the quality of the services that they can provide for today’s demanding manufacturers and even into the future with advanced engineering and design.
But ultimately, it’s not just a manufacturing process: It’s about the will and power of man to create something.
And so, as times and industries keep changing, so do the tools and ways of working to continue including CNC milling into manufacturing processes well into the foreseeable future.
Recent Comments